Microscale design.
Massive impact.
Microstructure lies at the heart of our approach to material design. Our machine learning algorithms leverage image data to characterise and optimise your materials faster and more accurately than ever before.
Image to insight.
Unprecedented accuracy and speed.
Our state-of-the-art machine learning segmentation tools can identify diverse and complex features in your microscopy images. Rapidly extract volume fraction particle morphologies, or identify particle cracking anomalies in a dataset of thousands of images. Our highly automated approach provides flexible, scalable and accurate analysis that continuously improves as your dataset grows.
And we aren't limited to 2D data. Our 2D to 3D reconstruction technology can be trained on a single representative micrograph, and has been validated on over 80 different materials. Leverage high resolution, easy to collect cross sectional image data to understand the 3D behaviour of your material system - from transport properties to mechanical behaviour, and beyond.
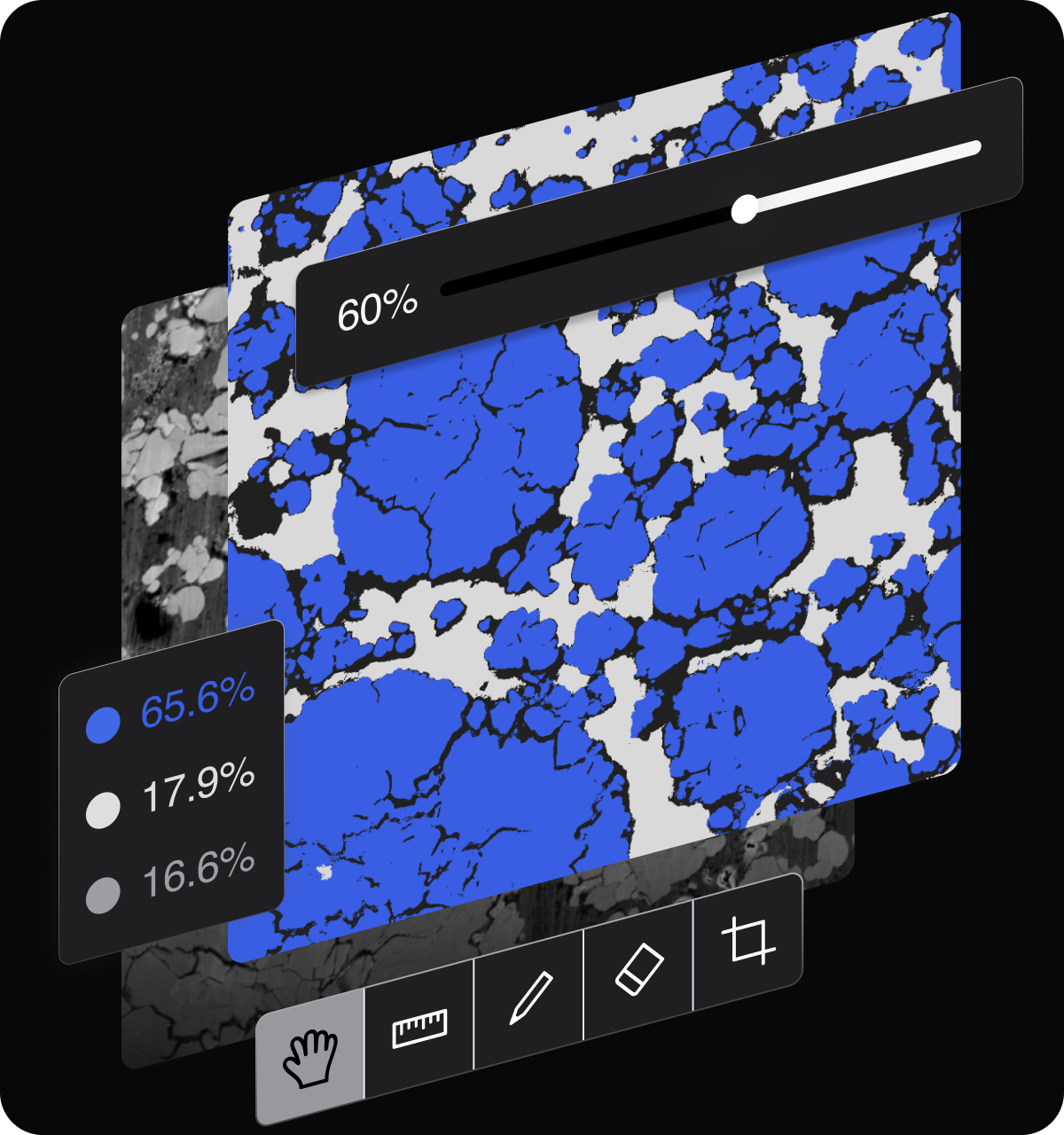
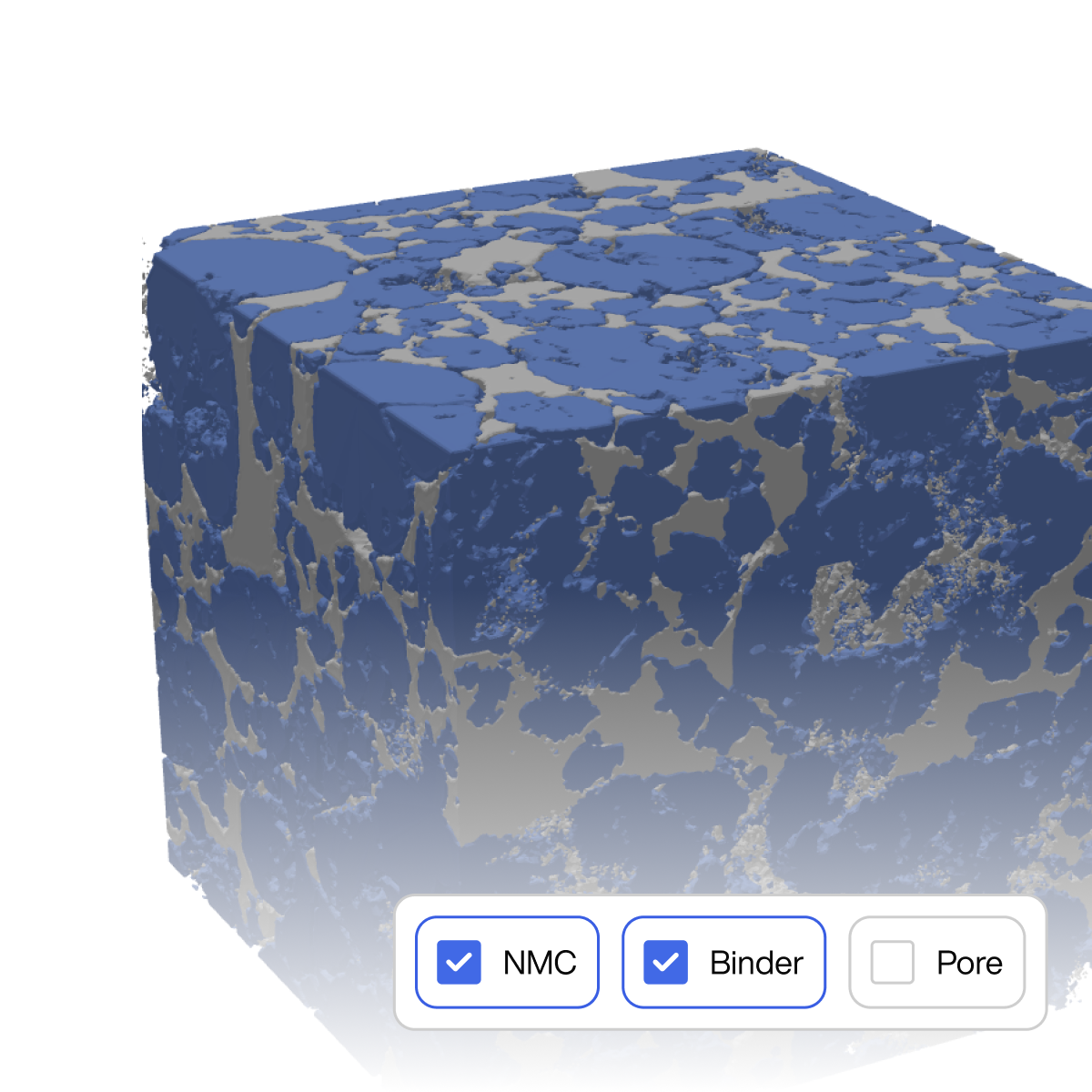
Microstructural design.
Supercharged with AI.
Material design is a highly complex challenge. At Polaron, we use microstructural data to bridge the gap between manufacturing processes and material performance.
Our exploration module allows the generation of microstructures with new properties. Make volumes with different phase surfaces areas, or graded phase volume fractions, in a matter of seconds and at the click of a button. Analyse the effects of these changes using our analysis capabilities, and unlock information about how different microstructures could perform.
Optimisation goes a step further, determining both the best microstructure for your use case and how to make it. Test thousands of potential microstructural designs in under a day to identify the best material manufacturing routes, or explore complex multi-objective design challenges, balancing performance, cost, and sustainability.
FAQs
Segmentation and 2D to 3D reconstruction models can be trained using a single micrograph, as long as it is large enough to capture the features you are interested in. Optimisation studies require between 3 and 50 images, depending on the number of process parameters to be explored. Micrographs must be cross sectional images of your material, but can be collected using a range of different imaging techniques e.g SEM, optical microscopes, EBSD. There are no specific magnification or resolution requirements - any features captured in your data will be analysed and included in the models.
Our algorithms have been validated on a broad range of materials, including alloys, battery materials, ceramics and more. The model learns solely based on the features in your data, and is thus largely material agnostic. See microlib.io for examples of reconstructions.
Segmentation allows users to extract statistical information about phase morphology, such as volume fractions, surface area, and correlation functions. Reconstruction allows users to perform 3D electrochemical and mechanical modelling to better understand how and why materials behave differently. New microstructures with a specific microstructural property (e.g. volume fraction) can also be predicted. Finally, optimisation allows users to directly determine the best manufacturing parameters for their material processing routes.
No - we understand that micrographs and processing data often constitute core IP for manufacturers. Any data you upload to Polaron is only used to train your private models, and is isolated from any users outside your organisation. Unlike many AI companies, Polaron does not develop centralised foundational models, instead training bespoke models from scratch on small datasets. This approach was designed to match the unique requirements of material manufacturing.
You can book a demo with one of our material science experts by following the link. We can then give you access to a demo and help you to understand how our tool can be integrated into your R&D workflows.
Request your personalised demo today!
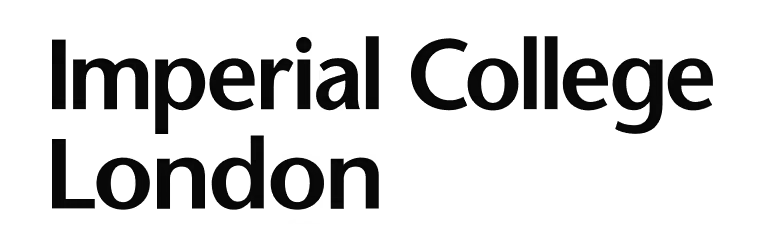
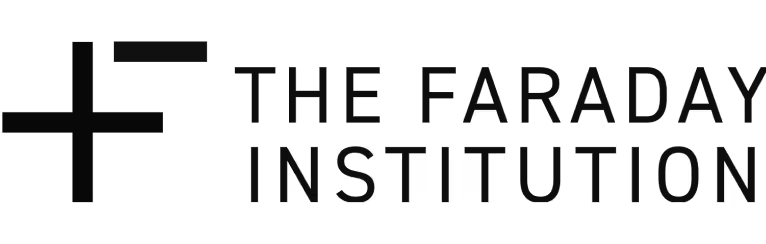
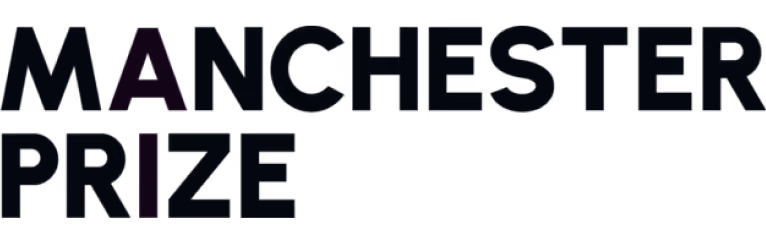
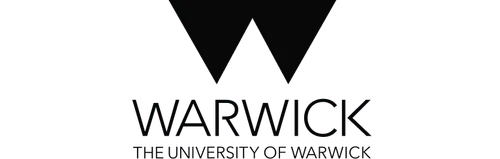